Leaning Truck?
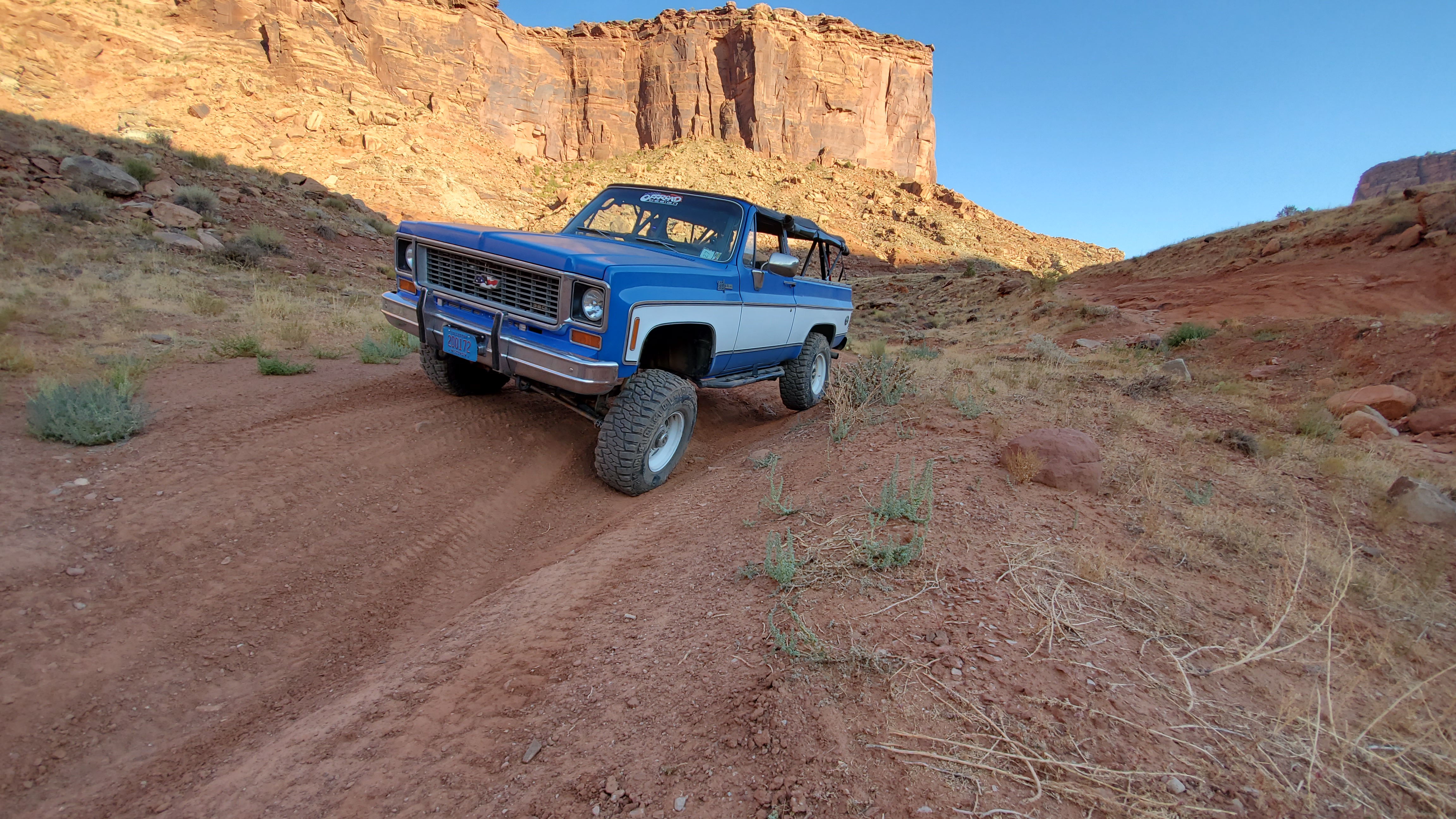
Below is a customer question about leaning springs and what to do to remedy the situation. We figured it could be helpful for many people:
A lean is fairly common and is a byproduct of a soft spring and kind of unique to this truck platform because the front springs’ mounting width is fairly narrow. A small difference in the height of the springs can make an exaggerated difference in side to side height and a small weight difference can also also cause an exaggerated ride height change. To put some numbers on it, the springs are about 32” center to center and the outside of the body where you see and measure is about 80”. The body has about 2.5:1 leverage over the springs so a ¼” change at the spring pad should convert to 5/8” at the body line. It also works the opposite for weight, any weight change has a big lever arm over the springs and makes itself look way bigger than it should.
We have yet to have a spring problem that was causing a lean so I’m betting your springs are just fine and we need to work out what else is going on. It is possible there’s a small variation in the spring height and if there is ¼” of difference (typically more than they vary) and the low side is on the heavy side of the truck it would amplify that weight difference. Simple solution (that’s not so easy to execute) is swap them side to side. This does a few things:
1: if there is a slight height difference in the springs you can put the taller spring on the heavy side of the truck and make a little improvement in the lean.
2: if there is a big height difference in the springs we know about it and can fix it.
3: if a large ride height problem follows the springs when they’re swapped side to side then we know it’s a spring problem.
Some deep background info on springs
The height of a spring under load is set by the spring’s rate and starting height. Spring rate is set (in a leaf spring) by the number of leaves and the thickness of each leaf along with spring length, some factors that have to do with construction technique and a material property (modulus of elasticity) that is essentially the same for all grades, types and heat treats of steel. Height under load is just the weight on it divided by the rate. The important detail here is that the variables that effect the springs performance are all very visible, measurable properties. Boiling it down, if a pair of springs has the same number of leaves, length of leaves, and thickness of leaves, they’re going to be the same rate. That’s a big important point. If the material has all the same measurable characteristics, it is the same rate. If the height is the same between the two, they will hold an identical load at the same height also.
The “hidden properties” are material grades and heat treating but their effect is seen in the strength of the material that will be apparent when the spring is at its highest stress point meaning at full load or bump travel. The way a weaker material or heat treat will become obvious is that the material won’t flex and spring back when loaded heavy, it will flex as far as it can and bend permanantly to some extent so it won’t return to it’s original arch. To illustrate, if your spring has 5” of arch when it’s brand new and you install it and take it to full compression and check it again, it should still have 5” of arch. If there is a material strength problem you may measure 4.5” of arch. The actual rate still didn’t change but the height that the spring will hold a load changed because it bent a little instead of just “flexing”.
So the way this translates to the real world and your leaning truck is that the spring rate itself is very unlikely to be the problem. Unless one side is missing a leaf or a spring is built with the wrong material thickness, they will be the same rate. This leaves 2 variables, the arch of the spring and the weight on it. The arch is easy to check when the springs are on the floor and it’s always a good idea to check them side by side when they’re new so you have a baseline height when it’s easy to check. Unfortunately it’s hard (virtually impossible) to check the free arch on the truck but it’s the only way to know if the spring height is the problem. This comes back to pulling the springs, measuring them and swapping side to side to see if a problem follows the spring. You might be able to read between the lines in all of this and say there is no reason to swap the springs side to side if you know the construction is the same and the height is the same but it is the ultimate test in proving if the lean follows the springs.
The last variable is the weight on the spring. There’s nothing that says any given truck is loaded the same on every corner and a softer spring will make a load change from one side to the other more apparent than a stiffer spring. This is something we run into fairly often: a guy’s old lift kit springs sat level but when he installs his ORD springs the truck has a lean. The old springs were stiff enough that the weight difference was not obvious but our springs make the weight difference apparent.
So, what to do?
If you can remove springs to measure and swap that’s a great start. If all the checks on the springs come out OK then it’s time to start adjusting things. The available options are (in no particular order):
Add a swaybar
Move weight around on the truck
Shim the springs to correct heights
Build custom springs with individual rates for the corner weights on the truck.
A relatively easy step is to put a swaybar on it (assuming you haven’t already) since the extra roll rate on the bar can help level the truck side to side. There’s also room to preload the bar a little if the end links are adjustable. If you have a swaybar installed, make sure it’s not bent and preloading the suspension the wrong way.
Moving weight around is sometimes pretty simple. If you have your toolbox tied down on the low side, move it to the high side and see what happens. Sometimes it’s not simple, like if your spare tire carrier is built to mount the tire offset to one side. Just look for the easy stuff and do what you can. If you want to get really official with this stuff, you can weigh the truck on each corner and have an idea what’s going on and what it would take to correct it.
It’s totally fine to fine tune things with some short shims between the spring and axle. With the narrow spring mounting on the front of most GM trucks, a little bit can go a long way and ¼” to 3/8” of shim under one side probably won’t be noticed by most people but will go a long way toward leveling the ride.
At the end, we can build custom spring systems with 4 individual different rate springs for each corner. This is getting pretty specialized but if you know your load is not centered it might be what needs to happen. The example that comes to mind is a K5 with a wheelchair lift